
Energy Management
We help you cut your energy costs !
Energy Management
STERIFLOW SAS has developped a strong expertise in reducing energy costs. Our solutions helped our customers to reduce significantly water and steam consumption.
According to the size of the installation, sterilization/ pasteurization, we are uniquely positioned to offer our customers complex or simple solutions.
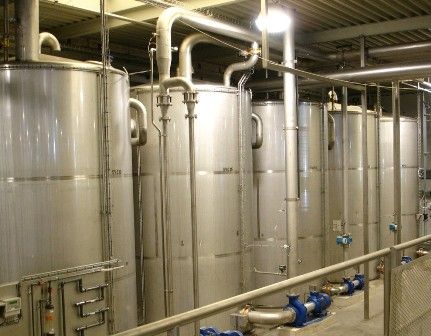
Energy and water management in the Steriflow industrial environment for pasteurization and sterilization
In a context where actions to limit energy consumption are required, Steriflow aims to propose sterilization solutions to increase productivity while saving energy and water. Reusing process water, condensate recovery and optimizing the use of heat are solutions offered to customers to save energy during sterilization cycles. The heat, once used is transferred to cooling water, so it is appropriate to recover energy.
Solutions to improve sterilization process
Steriflow has been working for over 40 years in the manufacture of industrial autoclaves and intends to maintain its leadership in the field. Inventor of the sterilization water cascading process, Steriflow knows, even more today than 10 years ago, that the sterilization processes must be constantly optimized to provide high-quality, efficient and non-energy consuming autoclaves. His expertise and studies in seeking improvements in the sterilization process for the agri-food and pharmaceutical sector make him a reference in innovation.
The first solution is the recovery of steam condensates (which still contain a lot of energy) a real energy gain because the water of the boiler does not need to heated by a fuel-inefficient system. In addition, these recycled condensates avoid the expensive chemical treatment of water to power the boiler. Second solution: the recovery of process water. This can be done as long as the products have not soiled this water too much. Third solution: the recovery of cooling water which, not being in contact with the sterilized product (cans, milk bottles, plastic trays, small pouches, …) can be recycled. It can then either be returned to a cooling tower, or be stored to preheat the autoclave during another cycle, for example.
Today, only the pump consumes electrical energy; this consumption is low because the pressure drop in the PLATULAIRE heat exchanger is limited.
How can we improve an energy balance?
The energy balance makes it possible to know the ratio between the quantity of energy expended to carry out an operation and the final energy actually available. An autoclave is a heat exchanger between packaged products and a controlled and controlled heat production system. It is also a huge generator of hot water during cooling operations, water discharged between 100 ° C (early cooling) and the ambient temperature. The heat provided during the sterilization or pasteurization cycle allows both to heat the products (cans, milk bottles, plastic trays, small pouches, …) and the autoclave. By improving the distribution networks, the heat input is optimized. This translates into boiler efficiency, lagging, purge reduction, fine and precise temperature and pressure control and optimization of process cycles. The energy balance can be further improved by reusing water, creating secondary heat exchanges, which will extract and reuse energy, before the final intake using a boiler during the heating and cooling tower during cooling, for example. The energy balance is above all a global approach for which technical and financial assessments of the environmental impact will lead to savings.
What possible reuse of cooling water in the plant?
The heat of cooling water can be recovered to produce water at 60 ° C. In order to save energy, it is possible to use this water in the factory for the cleaning or the operation of the sanitary, the washing, the maintenance in temperature of annexed areas like the biological water treatments, economy of energy during the cycles). Depending on the site, other uses may also be considered.
Usually done with water at room temperature or colder, the principle of staging cooling is a solution that allows to transmit the energy of the hot autoclave to different water, by splitting the cooling according to the temperatures.It is then possible to have, for example, a water reserve at 80 ° C, another at 60 ° C, one at 40 ° C … Once stored, the hot water is reused in pre-heating phase (which will be staged according to the same principle) by managing different water valves. The steam produced by the boiler will then intervene only at the end of heating for the autoclave with the products. Similarly, cooling by stage (first cooling with water at 60 ° C generating water at 80 ° C, 2nd with water at 40 ° C generating water at 60 ° C, etc …) , the cooling system (cooling tower or refrigeration unit) will no longer have to run at the end of cooling. The same water can therefore be used in a loop to preheat and then cool the autoclave. In this case, the energy balance is improved on water discharges, energy consumed during heating and during cooling, generating substantial savings.
Train the user of the Steriflow sterilization solution to optimize energy management and prevent energy loss.
Each industrial site has constraints and specificities (space, equipment, etc …). Steriflow focuses on a work methodology that puts the customer at the heart of its approach. A consulting phase allows to realize an energy balance taking into account the specificities of the chosen product (autoclaves dali, static, shaka, …), the number of autoclaves installed, the configuration (automation or not), the existing networks of regulations and the abundance. The main objective of the advice phase is to find the optimal function for the reuse of water. It takes between 2 and 4 days to make a balance sheet. Once this phase is complete, the conceptual phase comes into play, starting with the development of the PID, the specifications of the main equipment and the automation analysis. The completion time may vary depending on the complexity of the installation. The assessment of potential gains leads to a process of sterilization and recovery of water and energy saving (realized by the user).
In the midst of technological growth, and mainly the digitalization of production systems within the framework of innovative industry 4.0, Steriflow makes the choice of innovation.
Find all our solutions for sterilization by industrial autoclaves
Food solutions – Pharmaceutical solutions – R&D