
Gestion d’énergie
Nous vous aidons à réduire vos coûts énergétiques
Gestion d’énergie
Steriflow a développé une forte expertise dans la réduction des coûts énergétiques.
Avec nos solutions, nos clients ont réduit de façon importante leurs consommations de vapeur et d’eau.
En fonction de la taille de l’installation de stérilisation/pasteurisation, nous pouvons offrir des solutions simples ou complexes.
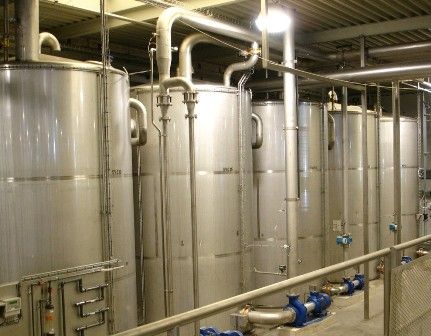
La gestion d’énergie et d’eau dans l’environnement industriel Steriflow pour la pasteurisation et la stérilisation
Dans un contexte où les actions à mener pour limiter la consommation d’énergie sont de rigueur, Steriflow s’attache à proposer des solutions de stérilisation permettant de gagner en productivité tout en faisant des économies d’énergie et d’eau :
- réutilisation des eaux de process,
- récupération des condensats,
- optimisation de l’utilisation de la chaleur,
sont des solutions proposées aux clients pour faire des économies d’énergie pendant les cycles de stérilisation. La chaleur, une fois utilisée est cédée à l’eau de refroidissement, c’est donc là qu’il est pertinent de récupérer de l’énergie.
Les solutions d’amélioration du processus de stérilisation
Steriflow œuvre depuis plus de 40 ans dans la fabrication d’autoclaves industriels et entend conserver sa place de leader dans le domaine. Inventeur du procédé de stérilisation par ruissellement d’eau, Steriflow sait, encore plus aujourd’hui qu’il y a 10 ans, que les procédés de stérilisation doivent être constamment optimisés pour mettre à disposition des autoclaves de haute facture, efficaces et non énergivores.
Son expertise et ses études pour la recherche d’améliorations dans le processus de stérilisation pour le secteur agroalimentaire et pharmaceutique font de lui une référence en matière d’innovation.
Première solution
La récupération des condensats de vapeur (qui contiennent encore beaucoup d’énergie) un véritable gain énergétique car l’eau de la chaudière n’a pas besoin d’être réchauffée par un système énergivore. De plus, ces condensants recyclés évitent le traitement chimique couteux de l’eau pour alimenter la chaudière.
Seconde solution
La récupération de l’eau de process. Celle-ci peut être effectuée tant que les produits n’ont pas trop souillé cette eau. Troisième solution : la récupération de l’eau de refroidissement qui, n’étant pas en contact avec le produit stérilisé (boites de conserves, bouteilles de laits, barquettes plastiques, petits pochons, poches…) peut être recyclée. Elle peut alors soit être renvoyée sur une tour de refroidissement, soit être stockée pour préchauffer l’autoclave lors d’un autre cycle, par exemple.
Aujourd’hui, seule la pompe consomme de l’énergie électrique ; cette consommation est faible car la perte de charge dans l’échangeur PLATULAIREÒ est limité.
Comment améliorer un bilan énergétique ?
Le bilan énergétique permet de connaitre le rapport entre la quantité d’énergie dépensée pour réaliser une opération et l’énergie finale réellement disponible.
Un autoclave est un échangeur de chaleur entre des produits emballés et un système régulé et contrôlé de production de chaleur. C’est également un énorme générateur d’eau chaude lors des opérations de refroidissement, eau évacuée entre 100°C (début de refroidissement) et la température ambiante.
La chaleur apportée pendant le cycle de stérilisation ou pasteurisation permet à la fois de chauffer les produits (boites de conserves, bouteilles de laits, barquettes plastiques, petits pochons, poches…) et l’autoclave.
En perfectionnant les réseaux de distribution, l’apport de chaleur est optimisé. Cela se traduit par l’efficacité de la chaudière, le calorifugeage, la réduction des purges, la régulation fine et précise en température et pression et par l’optimisation des cycles du process.
Le bilan énergétique peut encore être amélioré en réutilisant l’eau et en créant des échanges de chaleur secondaires. Ceci permettra d’extraire et de réutiliser l’énergie, avant l’apport final, à l’aide d’une chaudière lors de la chauffe et d’une tour de refroidissement lors du refroidissement, par exemple.
Le bilan énergétique est avant tout une approche globale pour laquelle les évaluations techniques et financières de l’impact environnemental permettront de réaliser des économies.
Quelle réutilisation possible de l’eau de refroidissement dans l’usine ?
La chaleur de l’eau de refroidissement peut être récupérée pour produire une eau à 60°. Afin de faire des économies d’énergie, il est possible d’utiliser cette eau dans l’usine pour le nettoyage ou le fonctionnement des sanitaires, les lavages, le maintien en température de zones annexes comme les traitements d’eau biologiques, économie d’énergie pendant les cycles). En fonction des sites, d’autres utilisations peuvent également être envisagées.
Habituellement réalisé avec une eau à température ambiante ou plus froide, le principe d’étager le refroidissement est une solution qui permet de transmettre l’énergie de l’autoclave chaud à différentes eaux, en fractionnant le refroidissement selon les températures. Il est alors possible d’avoir, par exemple, une réserve d’eau à 80°C, une autre à 60°C, une à 40°C…
Une fois stockée, l’eau chaude est réutilisée en phase de préchauffe (qui sera étagée selon le même principe) en gérant différentes vannes d’arrivée d’eau. La vapeur produite par la chaudière n’interviendra alors plus qu’en fin de chauffe pour l’autoclave avec les produits. De même, en refroidissant par étage (1er refroidissement avec l’eau à 60°C générant de l’eau à 80°C, 2ème avec l’eau à 40°C générant de l’eau à 60°C, etc …), le système de refroidissement (tour de refroidissement ou groupe frigorifique) n’aura plus qu’à fonctionner en fin de refroidissement.
La même eau peut donc être utilisée en boucle pour à la fois préchauffer, puis refroidir l’autoclave. L’amélioration du bilan énergétique porte dans ce cas sur les rejets d’eau, sur l’énergie consommée pendant la chauffe et pendant le refroidissement, générant des économies substantielles.
Former l’utilisateur de la solution de stérilisation Steriflow pour optimiser la gestion des énergies et éviter des déperditions énergétiques
Chaque site industriel dispose de contraintes et de spécificités (espace, équipements, etc…).
Steriflow s’attache à une méthodologie de travail plaçant le client au cœur de sa démarche. Une phase conseil permet de réaliser un bilan énergétique en prenant en considération :
- les spécificités du produit choisi (autoclaves dali, statique, shaka, …),
- le nombre d’autoclaves installés,
- la configuration (automatisation ou non),
- les réseaux de régulations existantes et du foisonnement.
La phase de conseil a pour principal objectif de trouver la fonction optimale pour la réutilisation de l’eau. Il faut compter entre 2 et 4 jours pour réaliser un bilan.
Cette phase terminée, la phase conceptuelle entre en jeu, commençant par l’élaboration du PID, les spécifications des équipements principaux et l’analyse d’automatisme. Le temps de réalisation peut varier en fonction de la complexité de l’installation.
L’évaluation des gains potentiels conduit à la réalisation d’un processus de stérilisation et de récupération d’eau et d’économie d’énergie (réalisée par l’utilisateur).
En plein essor technologique, et principalement la digitalisation des systèmes de production dans le cadre de l’industrie innovante 4.0, Steriflow fait le choix de l’innovation.
Retrouvez tous nos solutions pour la stérilisation par autoclaves industriels
Pour l’agroalimentaire – Pour la pharmaceutique – Pour la R&D